Drilling and Venting
managing the outcome of your project
Ensuring a safe environment
As galvanisers its important to us to have as much control going through the molten zinc process as possible as this gives us the best opportunity to ensure we deliver quality and integrity in the work we do for our clients.
Part of this process means that we need to use holes during galvanisation as they enable us to better control and manage the outcome and to ensure we exceed expectations for your project.
If there are any doubts about the positioning or the size of the holes to be drilled, our experts are always on hand for sound advice about specific objects. If you are unsure on best hole placement, feel free to either talk to our staff or leave the drilling completely in our hands. The size of the holes is always relative to the volume of the member being galvanised. We will always place holes as inconspicuously as possible and use the smallest possible hole in relation to what’s required.

Drilling:
With hot dip galvanisation, it is critical that the liquid zinc and pre-treatment liquids can flow freely in and out of the hollow parts of the object and for air to be allowed to escape. As a result, holes must be drilled in the right places prior to galvanisation.
venting:
If air gets closed in and cannot escape, or if liquid is left in the object, hazardous situations can result and there may be very serious consequences.
The temperature in a zinc bath is 450°C. The high temperature means that air pockets heat up rapidly and enclosed liquids start to boil, producing steam. If that heated air or the steam cannot escape, pressure increases rapidly to very high levels. The object may then crack, or even explode. Consequently, before the hot dip galvanization process begins, crucial checks take place to ensure there are enough inlet and outlet holes int the object at the right places.
Galvanising an object with poorly positioned holes or openings that are too small can also distort the object during the galvanisation process. The team at Galvanising HB follow a thorough preparation and safety process to ensure this doesn’t happen.
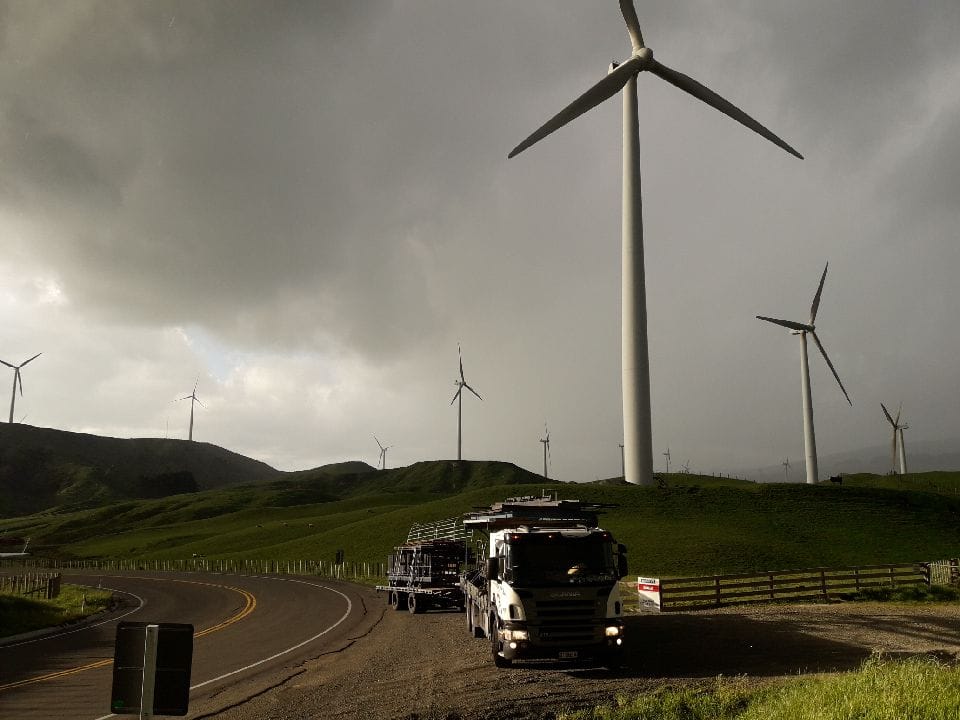
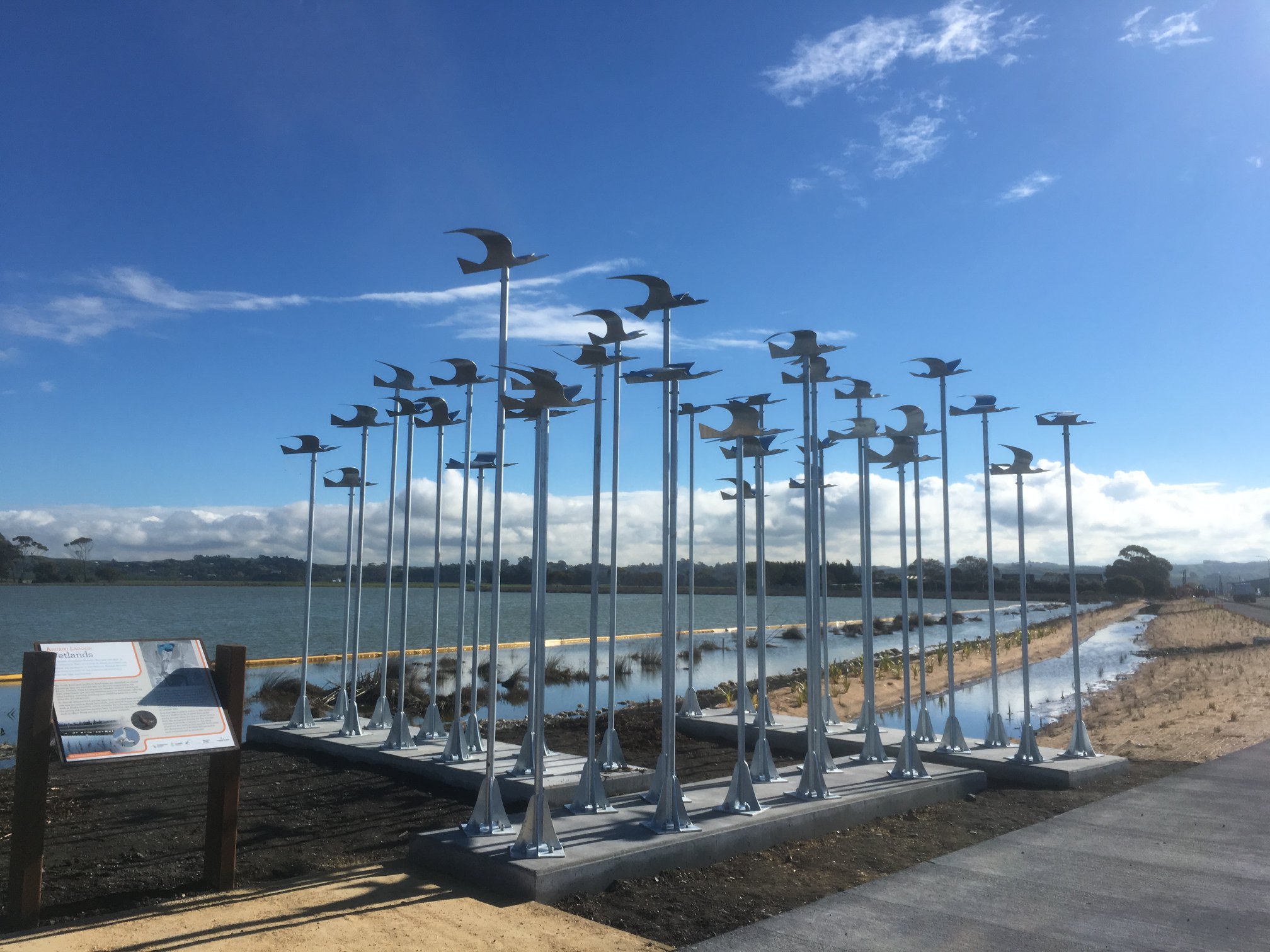
protecting product integrity
All items require thorough preparation; to allow for drainage and ventilation as well as rigging the steel correctly onto jigs.
To safeguard quality throughout the galvanisation process, objects need to comply with several conditions. Firstly, there must be enough holes in the objects to prevent air pockets and to allow the zinc to flow through the object freely. Molten zinc must be allowed to free flow without impediment. Hence openings must be large enough, without impairment of the structural strength for zinc to flow into the fabrication and out of it.
Secondly, where there are air pockets, pre-treatment will not work and so the object will not be galvanised in these places. If the excess zinc cannot flow out fast enough, zinc accumulates. In both cases, galvanisation quality suffers.
Since proper galvanising demands that inside, as well as outside, be completely cleaned and coated with zinc; air and ash must be allowed to flow upward and completely out, cleaning solutions and molten zinc must be allowed to flow through and completely cover the surface area. Simply stated, the structure must be lowered into the solution without trapping any air. It must also be raised from the solution without trapping any solution.
Consequently, ample passageways that allow flow in and out must be designed into the assemblies. Since items to be galvanised are immersed and withdrawn at an angle, the vent holes should be located at the highest point and lowest point in each hollow member. All components of fabricated hollow sections should be inter-connected with full open tee or with mitred joints. Each closed section must be provided with a vent hole and a drain hole.
Galvanising HB will visually identify the venting from the outside when assembly is received. This is necessary to check the adequacy of venting as well as to determine that it has not been omitted by mistake.
If you have any queries about the process, please connect with our team and we can help to clarify them for you.