acid, caustic cleaning
and pickling
preparing for the galvanising process
removing contaminants
For the galvanisation process to be effective it’s imperative that all organic contaminants such as dirt, paint markings, grease, and oil are removed from metal surfaces.
The galvanising reaction will only occur on a chemically clean surface. In common with most coating processes, the secret to achieving a good quality coating lies in the preparation of the surface. It is essential that surfaces are grease, dirt, paint and scale free before the galvanising process begins.
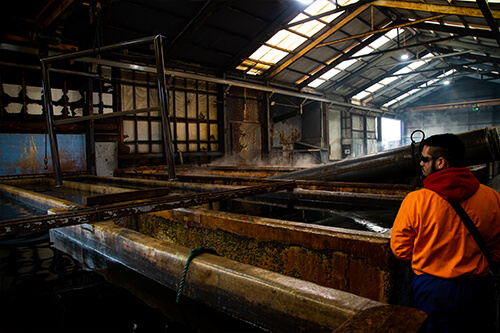
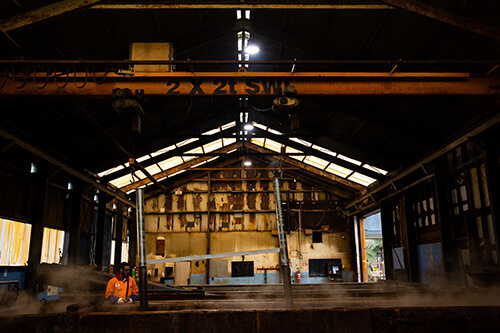
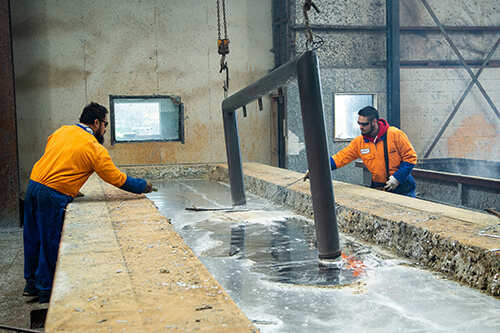
preparing for hot dip galvanising
For every stage of the process to work effectively oil, grease and paint must be removed.
Common practice is to degrease and to remove oils by first using an alkaline or acidic solution into which the object is dipped. This is known as caustic cleaning. The object is then rinsed in cold water to avoid contaminating the rest of the process. However, caustic cleaning will not remove paint except in rare circumstances and often paint will need to be removed or sand-blasted before work is sent to us. Welding slag and heavy grease may also need to be removed before work is received.
Scale and rust are removed from the steel surface by pickling in a dilute solution of hydrochloric acid at a temperature of about 155F. This process is called pickling and can take between 15-45 minutes depending on the material. Post pickling, objects are passed through a rinsing process to minimise contaminant carry-over to the next stage.
After further rinsing, the components will then commonly undergo a fluxing procedure. This is normally applied by dipping in a flux solution – usually about 30% zinc ammonium chloride at around 65-80°C. The fluxing operation removes the last traces of oxide from the surface and allows the molten zinc to wet the steel.
Galvanising HB can also offer their baths for cleaning or metal pickling only, removing the item from the process prior to zinc dipping